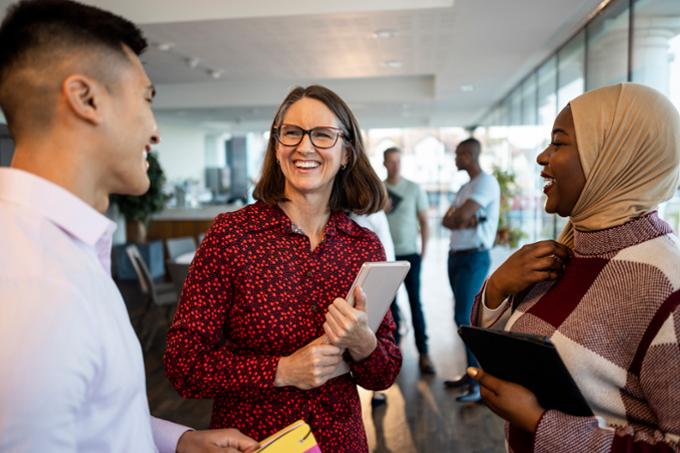
Centre for Experiential and Service Learning (CESL)
We know that learning happens best by doing.
At the Centre for Experiential and Service Learning we're here to help you learn by doing, which is what experiential learning is all about! You’ll have more opportunities to apply what you learn – not only in the classroom, but across campus, and in the wider community. This hands-on approach will help you retain what you learn and build valuable experience for your resumé and future employment.
Gain experience in both paid and volunteer positions. Graduate career-ready and find work fast!
What's in It for You?
- Workshops, programming, and campus events to gain skills specific to your goals and educational path.
- Digital badges that you can add to your resume and/or professional portfolios in areas such as career foundations, cultural awareness, leadership, and mentorship. Badges are designed to recognize the skills and opportunities students are participating in outside of the formal classroom.
- Transferable skills, knowledge, and experience to ensure you are career-ready when you graduate.
- ExpLORE for students is the Experiential Learning Opportunities, Resources, and Education Fund that is available to support students who are doing additional Experiential or Service Learning in or out of their classes and are requesting financial support. Review the fund description HERE for more information!
Contact Us
Centre for Experiential and Service Learning (CESL)
163 Riddell Centre
8:15 a.m. to 4:30 p.m.
Monday to Friday
Email: experiential.learning@uregina.ca
Volunteer Centre: volunteer@uregina.ca
Co-op/Internships: coop.office@uregina.ca
Ambassador Program: ambassadors.info@uregina.ca
All other inquiries: student.employment@uregina.ca
UR Path
UR Path is designed to help you succeed both in and outside the classroom through experiential learning opportunities. You’ll have more opportunities to apply what you learn – not only in the classroom, but across campus, and in the wider community. Graduate career-ready and find work fast by gaining experience.